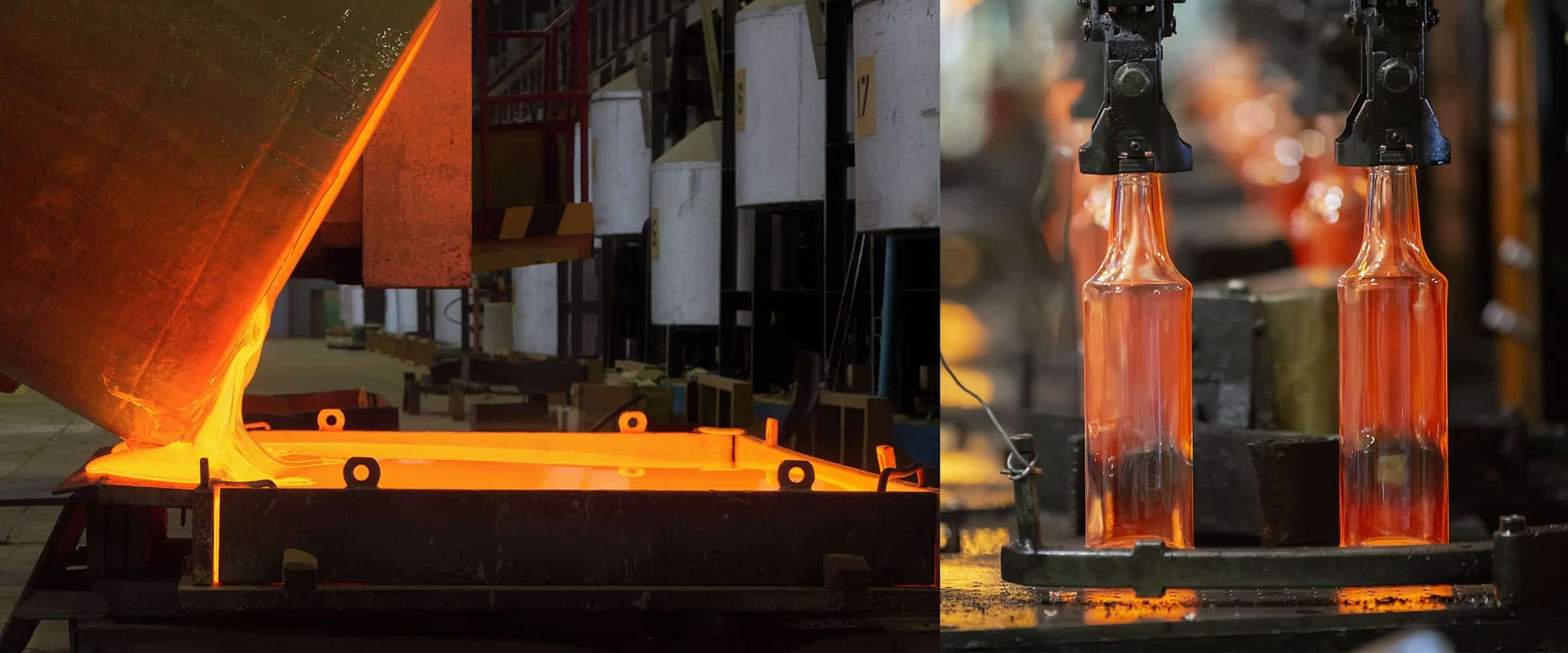
Glass Manufacturing
Modern glass manufacturing has undergone centuries of evolution. However, in recent decades, the Float Process method has become the dominant technique, responsible for producing 95% of the world’s glass. Each manufacturer’s float “line” varies, and production levels depend on the facility’s capacity and product demands.
Ingredients for glass
The glass manufacturing process involves the following steps:
Step 1: Batch mixing – In this step, the right ingredients are chosen. The most commonly used ingredients are silica (usually in the form of sand), soda ash, limestone, dolomite, feldspar, sodium sulfate, coal dust, and cullet (broken glass). These ingredients can be used in varying amounts to influence the finished product.
Step 2: Melting – The ingredients are melted at the hot end of a lehr inside a furnace heated to about 2800 degrees Fahrenheit. This turns the ingredients into a pliable molten gel.
Step 3: Floating – The molten gel is allowed to be added to a bath of molten tin, which is heated to around 1900º F. The glass floats on the top of the tin because the density of tin is far greater than molten glass. The ribbon of glass is then cooled down while still moving across the molten tin surface. When the glass surface is hard enough to avoid impressions by the roller, it’s removed from the bath. The speed at which the glass moves through the bath influences its dimensional characteristics.
Step 4: Annealing – The glass is carried over a long conveyor system to the annealing lehr and cooled off by air jets of decreasing temperature. By altering the curing procedure, manufacturers can create a different hardness to the glass. The glass is then washed and prepped for the final glass production step.
Step 5: Cutting – The final stage of glass production is known as capping. When the glass passes through the annealing lehr, it is cut by cross cutters, which slices through the glass. This allows the glass company to package each piece of glass into various sizes and shapes.
The float process’s key benefit is that it allows glass production to occur on a vast scale. The results are an excellent finished product that can be manipulated at all stages of the production process to create a wide array of glass products.